Retrofit pyrolýzně torifikační jednotky
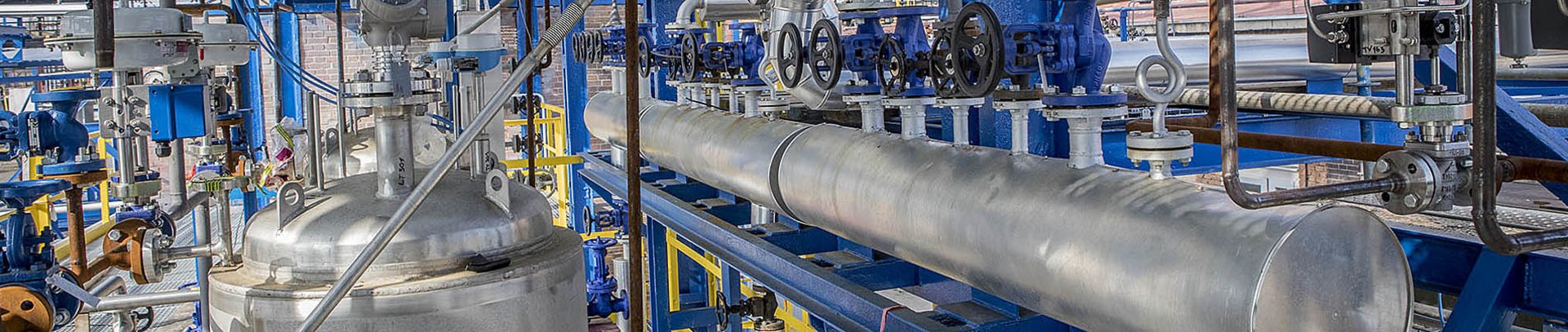
MODUL DOVYBAVENÍ LABORATOŘE – RETROFIT PYROLÝZNĚ TORIFIKAČNÍ JEDNOTY
Název zakázky Modul dovybavení výzkumné laboratoře
Termín realizace 2019
ZADÁNÍ
Projekt byl realizován na základě poptávky zákazníka a zkušeností s touto technologií pracovníků firmy Temex.
Hlavní požadavek zákazníka byl zaměřen na tzv. rekonstrukci původního zařízení a dodávku nových komponent dle zadání na vylepšení procesu.
ZÁKLADNÍ CHARAKTERISTIKA
Popis stávající pyrolýzně torifikačního zařízení
Jednotka (obrázek č. 1a,b) je zařízení, které slouží termické destabilizaci materiálů, bez přístupu oxidačních médií. Při provozu dochází k ohřevu materiálu nad mez termické stability přítomných organických sloučenin, přičemž dochází ke štěpení vazeb vysokomolekulárních látek na nízkomolekulární produkty a pevný zbytek. Tento proces probíhá v retortě pyrolýzně torifikační jednotky. Retorta se skládá z žáruvzdorné trubky a šneku s jádrem. Materiál retorty je žárupevná nerezová ocel AISI309 s tepelnou odolností do 1000 °C.
Teplo pro proces uvnitř retorty zabezpečují dva plynové hořáky spalující zemní plyn, kterých horké spaliny proudí v spalinovém vedení mezi retortou a vnějším opláštěním. je ohřívána plynovým hořákem. Teplota v retortě je řízena pomocí pěti řídících termočlánků. Hlavní částí retorty je šnek retorty, který slouží k posunu vstupujícího materiálu retortou a k jeho odplyňování. Šnek retorty je poháněn dvěma pohony o výkonu 2,2 kW.
Vyprodukovaný pyrolýzní nebo torifikační plyn je z retorty odváděn potrubím plynu do sekce chladičů, kde dojde k jeho zchlazení a zkapalnění kondenzovatelných podílů. Výstup pevného zbytku z procesu je řešen jako přepadový, z retorty do prvního vynášecího šneku koksového hospodářství. Koksové hospodářství je určeno ke zchlazení pyrolyzního nebo torifikovaného zbytku a bezpečné dopravě mimo technologii.
1. Úprava výstup pevného zbytku
V průběhu provozu poloprovozní termické jednotky Pyromatic 250, bylo zjištěno, že přepad pevného zbytku, který je koncipován jako zužující se trychtýř z důvodu napojení na následný vynášecí šnekový dopravník, nevyhovuje z důvodu častého klenbování pevného zbytku, čímž dochází k jeho úplnému ucpání a nucenému ukončení provozu.
1.1. Popis současného stavu výstupu pevného zbytku
Na přepad pevného zbytku (obrázek č. 1.1), který je zužující se, navazuje první nožové šoupátko ovládané tlakovým vzduchem. První nožové šoupátko se nachází mezi přepadem pevného zbytku a prvním vynášecím šnekovým dopravníkem. Kromě odsunu pevného zbytku přepadajícího z retorty, slouží vynášecí dopravníky také k jeho chlazení. Vynášecí šnekové dopravníky jsou koncipovány jako dvouplášťové s kapalinovým chlazením. Pohon vynášecích šneků je zabezpečen elektropohonem s převodovkou o výkonu 1,1 kW. Pevný zbytek pak postupuje do druhého chlazeného šnekového dopravníku a přes turniket do vážené nádoby na pevný zbytek. Vážená nádoba je umístěna na 4 tenzometrech s vyvedením informačního výstupu do řídícího PC. Mezi váženou nádobou a třetím vynášecím šnekovým dopravníkem se nachází druhé nožové šoupátko ovládané tlakovým vzduchem, pro oddělení obou pracovních prostorů. Třetím šnekovým dopravníkem je pevný zbytek odváděn do přepravní nádoby, která slouží k jeho odvozu. Pohon třetího vynášecího šnekového dopravníku je zabezpečen elektropohonem s převodovkou o výkonu 0,75 kW.
1.2. Popis úpravy výstupu pevného zbytku
Z důvodu častého klenbování pevného zbytku a ucpávání se přepadu pevného zbytku je naplánována úprava – rozšíření přepadu pevného zbytku a zároveň také úprava vstupu vynášecího šnekového dopravníku, který zabezpečuje odsun a chlazení vyprodukovaného pevného zbytku. Jedná se o rozšíření přepadu pevného zbytku na hodnotu průměru trubky, kde stěny přepadu budou rozšiřující se, aby se eliminovalo klenbování pevného zbytku. Tím se zabezpečí přepad z celého průřezu retorty a nedojde k přesypu pevného zbytku za přepadový otvor.
Na základě tohoto rozšíření přepadu, dojde také k úpravě – rozšíření vstupu a části chladící délky prvního vynášecího šnekového dopravníku. Dále do stěny vynášecího dopravníku bude usazený snímač teploty pevného zbytku, pro kontrolu jeho výstupní teploty z retorty jednotky. Snímač teploty bude usazen do stěny dopravníku, tak aby byl v blízkosti šneku z hlediska citlivosti měření, ale aby nemohlo dojít k jeho poškození od rotujícího šneku a posouvajícího se pevného zbytku. Snímač teploty musí být v protiexplozivním provedení. Teplotní snímač bude přímo připojen na doplněnou měřící kartu Simatic 6ES7331-7KF02-0AB0 v rozvaděči RM6. Karta Simatic 6ES7331-7KF02-0AB0, která bude umístěna v rozvaděči RM6, je součástí dodávky zakázky. Rozsah teplotního snímače bude 0 – 800 °C (termočlánek typ K). Doporučujeme použití snímače od ZPA Nova Paka, které jsou již použity na technologii a jsou s nimi dobré zkušenosti. V průběhu úprav dojde také ke kontrole stavu utěsnění a uložení prvního i druhého vynášecího šnekového dopravníku a jejích potřebnému servisu.
Rovněž dojde k částečné úpravě základového rámu v místě přepadu pevného zbytku a vynášecího šnekového dopravníku, dle prostorových potřeb.
První nožové šoupátko, které se nacházelo mezi přepadem pevného zbytku a prvním vynášecím šnekovým dopravníkem, bude přesunuto z důvodu jeho velikosti a možnosti opětovného použití, mezi výstup prvního vynášecího šnekového dopravníku a vstup druhého vynášecího šnekového dopravníku. Bude patřičně upravena trasa hadic ovládacího tlakového vzduchu pro pneumatický válec, který ovládá nožové šoupátko. Po demontáži nožového šoupátka proběhne kontrola jeho stavu, výměna těsnění a následný komplexní servis včetně seřízení koncových snímačů.
Dále dojde k odstranění turniketu z cesty pevného zbytku, z důvodu jeho častého zasekávání se. Vzhledem k této změně dojde následně k úpravě systému propojení váženého uhlíkového boxu a druhého vynášecího šnekového dopravníku pro vstup pevného zbytku z dopravníku do boxu, který může být o teplotě až 200 °C. Nový systém propojení tak musí umožňovat jejich plynotěsné spojení, teplotní odolnost minimálně do 200 °C, možnost dilatace tak aby zároveň neovlivňoval vážící tenzometry uhlíkového boxu. Stejný systém propojení bude použit pro spojení váženého uhlíkového boxu a třetího vynášecího šnekového dopravníku, který dopravuje pevný zbytek do transportního kontejneru pro jeho odvoz.
2. Ohřev pyrolýzně torifikační jednotky
V průběhu provozu termické jednotky Pyromatic 250, bylo rovněž zjištěno, že rozdělení tepla je zejména ve středové části jednotky nerovnoměrné. Z toho důvodu nedochází k optimálnímu provozu a zabezpečení jeho konstantní teploty, co má vliv na výstupní produkty procesu.
2.1. Popis současného stavu ohřevu pyrolýzně torifikační jednotky
V současné době zabezpečují ohřev retorty pro vlastní proces pyrolyzních a torrifikačních vstupních surovin, dva plynové hořáky spalující zemní plyn. Hlavním hořákem umístěným na začátku v 1/3 délky pyrolýzně torifikační jednotky je monoblokový plynový hořák s vlastním ventilátorem spalovacího vzduchu a regulátorem tlaku plynu RA – HP1 – 06 (tabulka č. 2.1 a obrázek č. 2.1).
Druhým pomocným hořákem pro dohřívání zadní části retorty, umístěný ve 3/3 délky pyrolýzně torifikační jednotky a temperovaného výstupního potrubí je plynový hořák Thermjet TJ 0015 (tabulka č. 2.2 a obrázek č. 2.2) s vlastním externím ventilátorem spalovacího vzduchu a regulátorem tlaku plynu. Oba hořáky jsou osazeny nerezovou výstupní tryskou pro maximální dosažitelnou teplotu 950 °C.
Tabulka č. 2.1: Technické parametry hlavního hořáku
Typ hořáku | RA – HP1 – 06 |
Výrobce hořáku | Eclipse |
Výkon hořáku minimální | 15 kW |
Výkon hořáku maximální | 600 kW |
Minimální tlak plynu na vstupu | 5 kPa |
Zapalování | Přímé, zapalovací svíčkou |
Detekce plamene | UV scanner |
Palivo | Zemní plyn |
Výkon ventilátoru spalovacího vzduchu | 1,1 kW |
Napětí ventilátoru spalovacího vzduchu | 400 V, 50 Hz |
Tabulka č. 2.2: Technické parametry pomocného hořáku
Typ hořáku | Thermjet TJ 0015 |
Výrobce hořáku | Eclipse |
Výkon hořáku minimální | 2 kW |
Výkon hořáku maximální | 44 kW |
Minimální tlak plynu na vstupu | 2 kPa |
Zapalování | Přímé, zapalovací svíčkou |
Detekce plamene | Ionizačnísvíčka |
Palivo | Zemní plyn |
Výkon ventilátoru spalovacího vzduchu | 0,37 kW |
Napětí ventilátoru spalovacího vzduchu | 400 V, 50 Hz |
2.2. Popis úpravy ohřevu jednotky
Tento problém nerovnoměrného rozložení tepla po délce retorty bude vyřešen přidáním dalšího zdroje tepla. Je uvažován jeden plynový hořák na zemní plyn o maximálním výkonu 198 kW, který by byl umístěn v 2/3 délky pyrolýzně torifikační jednotky. Uložení tohoto hořáku by bylo stejné jako u současných plynových hořáků, zapouzdřením a vyztužením nového uchycení hořáku do stávající izolační kazety. Tyto izolační kazety slouží k vytvoření spalinové cesty pro odvod spalin ohřevu, které zároveň odevzdávají teplo retortě uložené uvnitř izolačních kazet. Izolační kazety zároveň slouží jako první tepelně izolační vrstva, pro zamezení tepelných ztrát. V průběhu úprav na izolaci a navařování nového vstupu pro přidávaný hořák, budou zkontrolovány ostatní dva vstupy, zda nedošlo při jejich delším používání k poškození. V případě poškození dojde k jejich opravě a vyztužení. V tabulce č. 2.3 jsou uvedeny parametry možného navrženého typu hořáku na ohřev.
Tabulka č. 2.3
Typ hořáku | 4485 – 5B |
Výrobce hořáku | Fives |
Výkon hořáku minimální | 20 kW |
Výkon hořáku maximální | 198 kW |
Minimální tlak plynu na vstupu | 3,4 kPa |
Zapalování | Přímé, zapalovací svíčkou |
Detekce plamene | Ionizačnísvíčka |
Palivo | Zemní plyn |
Výkon ventilátoru spalovacího vzduchu | 1,1 kW |
Napětí ventilátoru spalovacího vzduchu | 400 V, 50 Hz |
V průběhu této úpravy tak dojde k hlavním změnám na zmiňované izolační kazetě, kde dojde k vytvoření vstupu pro plynový hořák. Následně dojde k úpravám na druhé izolační vrstvě a zakrytování jednotky. Další úpravy budou provedeny na přívodním plynovém potrubí, kde dojde k napojení přidávaného hořáku včetně ovládacího a bezpečnostního příslušenství. Zároveň bude nutná úprava a doplnění nové silové a regulační kabeláže pro doplňovaný plynový hořák, včetně úpravy nadřazeného softwaru řízení pyrolýzně torifikační jednotky – Simaticu a vizualizace ovládání. Pro možnost blízké montáže elektrického rozvaděče nového plynového hořáku, budou přesunuty centrální skřínky detektorů plynů.
V průběhu úprav na spalinovém vedení a kazetách dojde také k výměně poškozeného prvního snímače teploty pro měření teploty spalin a v případě poškození i jeho jímky. Poškozený první snímač teploty (a jímka) se nachází na horní straně izolační kazety, pod provozní násypkou jednotky. Teplotní snímač i náhradní jímka jsou již zakoupené
3. Vodní chladiče a doplnění měřících prvků
Vodní chladiče slouží ke zchlazení produkovaného pyrolyzních a torifikačních plynů a následné kondenzaci kapalných uhlovodíků a vodní páry, které zkapalňují při dané teplotě a tlaku v jednotlivých stupních vodních chladičů.
3.1. Popis současného stavu
Za vzduchovým chladičem následuje první vodní chladič s vlastní nádobou pro odběr kapalných produktů. V tomto chladiči by měly kondenzovat vyšší uhlovodíky. Následuje druhý vodní chladič, který má odvod kapalných uhlovodíků napojený na třetí vodní chladič, kde kromě lehčích uhlovodíků kondenzuje také vodní pára. Do společné odběrné nádoby se tak v současnosti dostává a míchá kapalina z druhého i třetího chladiče (obrázek 3.1.). V současnosti rovněž není propojovací potrubí mezi chladiči osazeno snímači teploty a tlaku, co zhoršuje celkové bilancování procesu.
3.2. Popis navrhovaného stavu
Pro možnost lepšího vyhodnocení materiálových a energetických bilancí provozu jednotky dojde k rozdělení výstupu kapaliny z druhého vodního chladiče a třetího vodního chladiče, který je v současnosti společný. Nový výstup kapaliny ze druhého chladiče bude doplněn o můstkovou váhu, která bude měřit hmotnostní přírůstek vyprodukované kapaliny, nožový šoupátkový uzávěr ovládaný pneumaticky s elektrickými koncovými snímači a pružné potrubní propojení výstupu kapaliny spolu s nádobou pro uchování produkované kapaliny. Kromě výroby a doplnění nového výstupu kapaliny z druhého vodního chladiče dojde také k úpravě propojovacího plynového potrubí mezi druhým a třetím vodním chladičem, tak aby potrubí umožňovalo proudění plynu, ale aby kapalina z druhého vodního chladiče nestékala po stěnách propojovacího potrubí do nádoby do kapaliny třetího vodního chladiče. Součástí tohoto propojovacího potrubí musí být také kovový kompenzátor, který bude vyrovnávat tepelné dilatace potrubí.
Můstková váha musí být v protiexplozivním provedení, s váživostí do 300 kg a přesností vážení 100 g. Součástí bude externí indikátor pro místní ovládání a kontrolu stavu váhy. Externí indikátor musí být také v protiexplozivním provedení a bude umístěn ke stávajícím externím indikátorům od stávajících vah. Vzhledem k dobrým zkušenostem a spolehlivosti, doporučujeme použití stejného typu váhy, jako jsou již osazené, z důvodu kompatibility s řídicím systémem a také stejného ovládání při její obsluze (tabulka 3.1.) Výstup váhy musí být 4-20 mA, pro napojení do stávajícího systému.
Tabulka č. 3.1: Technické parametry stávajících můstkových vah
Typ můstkové váhy | TGN 300 |
Výrobce můstkové váhy | Kadlec váhy |
Váživost váhy | 300 kg |
Přesnost vážení | 100 g |
Zpracování vážních dat | 4-20 mA (0-10 V, RS232, RS458) |
Rozměry můstku váhy | Nerezová ocel |
Pracovní prostředí | S nebezpečím výbuchu – ATEX |
Indikátor váhy | Externí – provedení ATEX |
Pro řízený odvod pyrolyzní nebo torifikační kapaliny ze stávajících chladičů slouží pneumaticky ovládaná nožová šoupátka. Pro novou instalaci jímání pyrolyzní nebo torifikační kapaliny je vhodné použít taktéž pneumatického nožové šoupátka, pomocí dvojčinného pneuválce s osazením snímačů koncových poloh v nevýbušném provedení – ATEX. Výstupní signál ze snímačů bude vyveden do nadřazeného řídicího systému Simatic a jejich signály budou zobrazovány ve vizualizaci. Součástí bude také úprava vizualizace s doplněním nově přidaných zařízení – vizualizace Control web 7. K novému nožovému šoupátku bude přiveden tlakový vzduch o maximálním tlaku 8 bar, z pneumatického rozvaděče (viz obrázek 3.4) pomocí tlakových hadic. V centrálním pneumatickém rozvaděči bude pro ovládání doplňovaného šoupátka, použitý neobsazený – rezervní vzduchový elektroventil. Rovněž bude upravena vizualizace pro možnost jeho ovládání z centrálního velínu.
V průběhu úprav bude také proveden servis stávajících nožových šoupátek, jejich vyčištění, výměna těsnících, kontrola a seřízení koncových snímačů. V Tabulce č. 3.2 jsou uvedeny parametry použitých šoupátek na stávající jednotce.
Tabulka č. 3.2: Technické parametry stávajících nožových šoupátek
Typ nožového šoupátka | L15 |
Výrobce nožového šoupátka | Fluidtechnik Bohemia |
Jmenovitá světlost | DN 200 |
Jmenovitý tlak | PN 10 |
Rozsah pracovní teploty | -10 °C až + 200 °C |
Materiál ucpávky | Viton |
Materiál tělesa | Nerezová ocel CF8M |
Materiál desky | AISI 316 |
Ovládání desky šoupátka | Pneumatické |
Pracovní tlak vzduchu | 6 – 8 bar |
Pracovní prostředí | S nebezpečím výbuchu – ATEX |
V průběhu odstávky z důvodu vykonání hlavních uvažovaných změn a úprav dojde také k doplnění teplotních a tlakových měřících prvků ve vstupních a výstupních potrubích jednotlivých chladičů:
a) Doplnění snímače teploty a tlaku do propojovacího plynového potrubí mezi prvním a druhým vodním chladičem. Snímač tlaku musí být v protiexplozivním provedení s výstupem 4 – 20 mA. Rozsah tlakoměru bude -6 až +6 kPa. Teplotní snímač bude přímo připojen na doplněnou měřící kartu Simatic 6ES7331-7KF02-0AB0 v rozvaděči RM6 a rozsah teplotního snímače bude 0 – 300 °C (termočlánek typ K).
b) Doplnění snímače tlaku do propojovacího plynového potrubí mezi druhým a třetím vodním chladičem. Tlakový snímač musí být v protiexplozivním provedení s výstupem 4 – 20 mA. Rozsah snímače bude -6 až +6 kPa.
c) Doplnění snímače tlaku do výstupního plynového potrubí ze třetího vodního chladiče. Tlakový snímač musí být v protiexplozivním provedení s výstupem 4 – 20 mA. Rozsah snímače bude -6 až +6 kPa.
d) Doplnění snímače teploty do propojovacího potrubí chladícího média mezi prvním a druhým vodním chladičem. Vzhledem k blízkosti přírubových spojů plynových potrubí plynu, musí být snímač teploty v protiexplozivním provedení s výstupem 4 – 20 mA. Rozsah teplotního snímače do 100°C.
Doporučujeme použití snímače od ZPA Nová Paka, které jsou již použity na technologii a jsou s nimi dobré zkušenosti.
Následně bude doplněná potřebná silová a datová kabeláž pro doplněné snímače. Elektrický rozvaděč bude doplněn o nové převodníky signálů měřících prvků a dojde k úpravě řídícího softwaru Simatic a vizualizace jednotky.
4. Úprava vodního chladiče
V průběhu úprav a změn na technologii, bude zkontrolován třetí vodní chladič, z důvodu jeho možného poškození. Bylo zjištěno že se do plynové trasy dostává chladící kapalina. Toto může být způsobeno prasklými svary v chladících trubkách. V případě že nebude možné tuto závadu odstranit, bude třetí chladič vyměněn za nový trubkový chladič. Typ a velikost nového chladiče bude minimálně srovnatelný se stávajícím chladičem.
5. Dopalovací komora pyrolyzního nebo torifikačního plynu
Pro potřeby likvidace pyrolyzního nebo torifikačního plynu bude do technologie termického využití organických materiálů zařazena dopalovací komora. K návrhu spalovací komory pro spalování vyrobeného plynu se předpokládá ochlazený plyn, který může byt znečištěn uhlovodíkovými sloučeninami – dehty. Předpokládané parametry plynu jsou uvedeny v tabulce č. 5.1.
Tabulka č. 5.1: Složení plynu z jednotky Pyromatic 250
Složení plynu | |
---|---|
H² [% vol] | 10 - 21 |
CO² [% vol] | 5 - 18 |
CO [% vol] | 2 - 15 |
CH4 [% vol] | 5 - 50 |
C²+ [% vol] | < 25 |
N² [% vol] | 0,2 - 5 |
Prach [g.m-³] | max. 5 |
Dehet [g.m-³] | < 20 |
Výhřevnost [MJ.m-³] | 5 - 40 |
Teplota [ºC] | cca 30 |
Přetlak [kPa] | 1,5 až 7 |
Objemový průtok plynu záleží na povaze zpracovávaného materiálu a nastavení procesních parametrů. Lze tedy předpokládat, že se bude pohybovat v rozmezí od 2 - 40 m³/hod. Účelem spalovací komory bude likvidace plynu bez využití tepla v podružných instalacích. Při návrhu a realizaci spalovací komory je nutno počítat s umístěním ve venkovním prostředí.
Komora bude vybavena hořákem pro zapalování a stabilizaci plamene na zemní plyn. Zemní plyn je přiveden k místu realizace. Součástí dodávky jsou veškeré potřebné armatury apod. (plynová řada) nutné pro správnou a bezpečnou funkci zařízení, hlídání plamene, el. rozvaděč potřebné revize, uvedení do provozu a zaškolení obsluhy.
El. energie a zemní plyn pro zapalovací a stabilizační hořáky a pro ventilátor spalovacího vzduchu budou přivedeny k místu realizace v požadovaných parametrech.
Součástí dodávky spalovací komory budou všechny potřebné zařízení a díly nutné pro správnou a bezpečnou funkci zařízení, s provedením potřebných izolací (vyzdívek) a nátěrů. Pro monitoring spalovacího procesu bude komora vybavena potřebnými čidly s vyvedením dat do stávajícího systému vizualizace.
Vzhledem k možné kondenzaci zbytkové vlhkosti ve vyrobeném plynu se doporučuje přívodní potrubí k plynu zaizolovat a opatřit odkalováním.
Vzhledem k poměrně vysokému regulačnímu rozsahu komory pro spalování plynu a možnému kolísání složení plynu (k tomu může docházet zejména při mimoprovozních stavech pyrolýzně torikačního zařízení, kdy nemá produkovaný plyn stabilní složení) se předpokládá jeho „seřízení“ (ev. úpravy) při uvádění do provozu.
Pro odvod spalin bude součástí dodávky systém odvodu spalin v provedení nerez.
6. Úprava a doplnění elektro části
V jednotlivých částech tohoto dokumentu byly popsány a doporučeny různé typy tlakových a teplotních snímačů a dalších doplňovaných zařízení, které potřebují pro svoji funkčnost přivedení napájení a vstup i výstup řídících signálů. Tedy nedílnou součásti doplnění elektro části jsou také silové a datové kabely, chráničky kabelů, úpravy a doplnění kabelových lávek, jistící a spínací prvky a další elektro prvky potřebné pro bezpečný a bezporuchový provoz těchto doplňovaných zařízení. Součástí bude také úprava vizualizace s doplněním nově přidaných zařízení – vizualizace control web 7.
Z rozvaděče RM6 (obrázek č. 6.1) bude z důvodu již plné konfigurace modulů Simatic přemístěn jeden modul digitálních výstupů do rozvaděče RM5 (obrázek č. 6.2) a na jeho místo se osadí nová doplňující výše uvedená měřící karta analogových vstupů 7KF02. Nutné bude i doplnění kabeláže vedoucí k přemístěnému modulu digitálních výstupů mezi RM6 a RM5, rekonfigurace systému SIMATIC (sdílení dat mezi systémy přes Profibus) a vizualizace.
V rozvaděči RM5 a RM6 budou doplněny odpovídající ochranné prvky a oddělovací relé technologie SIMATIC v souladu se stávajícími napájecími a ochrannými obvody.
Klíčové benefity našeho řešení:
- Vývoj a výzkum speciálních zařízení s Univerzitou VŠB