Renovation of liquid glucose lines
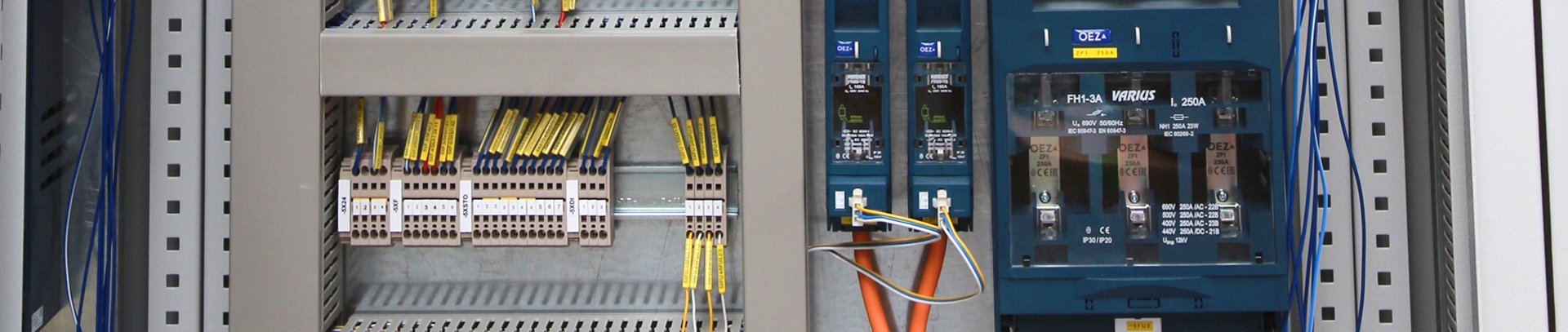
RENOVATION OF LIQUID GLUCOSE LINES FOR KOFOLA, Mnichovo Hradiště
Name of contract: ENDRESS+HAUSER – Renovation of liquid glucose lines for KOFOLA
Term of delivery: 2019
SPECIFICATION
The equipment is used for pumping liquid glucose into tanks from tankers and from there for further processing into syrup as required by the operator.
SOLUTION
The implementation documentation of electrical and M&R (measurement and regulation) was prepared for this project. The implementation of the work itself was then carried out based on this documentation.
DESCRIPTION OF THE AUTOMATED PROCESS
1. M&R switchboard for controlling the technological process
There is one suction pump and two discharge pumps. The pumps are controlled based on the operator’s requirement. The requirement is entered in the operator panel.
The flow in the individual branches is measured. For safety reasons, the maximum level in the tanks is monitored by means of level limit switches. The level limit switches also monitor the minimum level in the tanks to prevent the pumps from “going dry”.
The maximum pressure is also monitored here using pressure limit switches.
The individual branches contain shut-off valves. Each of these valves contains a solenoid coil. A programmed control algorithm is used to maintain control of the system. There are a total of 4 GT1-GT4 tanks.
Because these components are used in the food industry, all of them must be stainless steel (switchboard, cable routes, sensors, etc.)
According to technological procedures, the lines must be regularly sanitized, and so an electrical connection is made to the CIP DIVERSEY switchboard. At the same time, it is necessary to connect the new technology to the existing technology (current SYRUP EVAPORATOR switchboard).
A printer is located next to the switchboard and prints out a label after each issue or receipt.
2. Tanks for isoclugose and dissolved sugar
3. Screen of KTP700 Basic HMI panel – main window
The main window shows all the currently operating pumping equipment.
4. Suction – pump 1
5. Boiling tank
6. Discharge – pump 2, 3
7. Obrazovka HMI panelu – Servis
8. Label printer
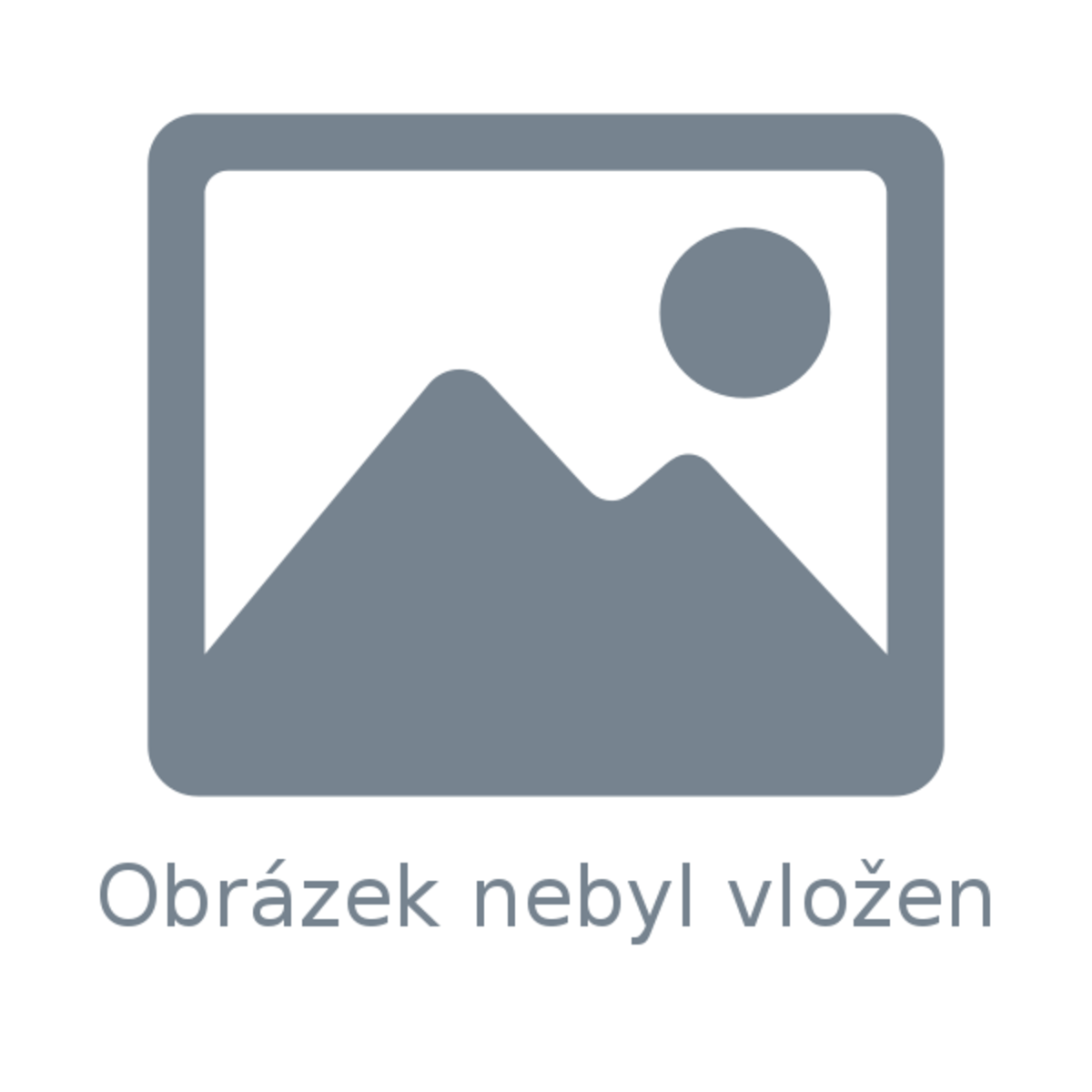
BASIC CHARACTERISTICS
Three pumps (1 suction, 2 discharge) are used to pump isoglucose or dissolved sugar into the tank.
During this pumping operation, the system automatically records the volume pumped and the status of the tanks.
Pumping requires the operator to set the line, from where and to where the pumping will be done, on the control operator panel. The correct setup of the piping is not checked by this system and must therefore be managed by the operator.
Key benefits of our solution:
- Economical operation
- Minimal failure rate
- Elimination of work-related accidents